Castings
We have ferrous metal castings using Investment casting and Foam casting technology. We are equipped with related machineries like induction furnace, spectrometer, temperature and other controllers.
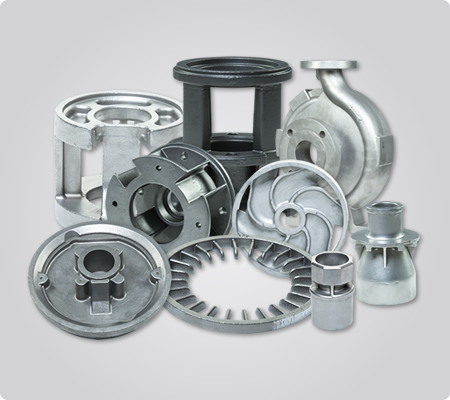
Investment Casting Lost wax technology
All types of, Pumps & valve parts, Hardware Products, Auto & automotive parts, Critical Aerospace & Defense Parts, pipe fittings products, Food machinery parts, Forged flanges & pipe fittings products, all types of General engineering and machining parts as per customer’s specification and drawings, etc.
Foam Casting Lost Foam Technology
- Innovative possibilities in design engineering
- highly complex component designing
- flexible integration of secondary functions
- reduction of material and weight
- undercuts and ducts
- no backdrafts needed
- high flexibility with regard to changes
Production :- Investment Casting Capacity up to 150 MT. Per month& Foam Casting Capacity is up to 50 MT. Per month
Heat treatment: Can be done with Customer Specifications
Quality: We meet our clients demands for better and uniform quality castings through our own very carefully formulated work practice programme
Other Facilities: Electro Polishing, Shot Blasting , H eat treatment process Etc.
Packaging: Packaging and labeling are also available
Materials: Manufactured at Alka,
Austenitic Stainless Steel : CF8, CF8M, CF8C, CF3, CF3M
Martensitic Stainless Steel : CA15 (410), CA40 (420) Special Alloys, as per Customer specification or International Standard Specifications like; ASTM, DIN, SAE & AISI.
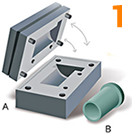
Tooling and Pattern Making
A tool is built to customer- provided specifications (A). Cold wax wax is then injected into the tool to create a wax
pattern/prototype (B) that will hold precise dimensional requirements in the final casting.
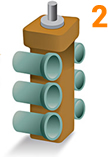
Pattern Assembly
The wax patterns are assembled onto the sprue.
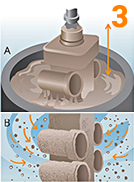
Dipping and Coating
Successive layers of ceramic (A) and stucco (B) are applied to the sprue assembly to form a hard shell.
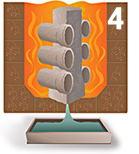
De-Waxing and Firing
The molds are flash- fired to remove the wax and sprue materials and then heated to 1,800° and placed on a sand bed, ready for pouring.
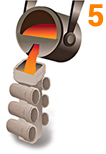
Casting
Molten metal, up to 3,000°, is poured into the hollow mold and then cooled.
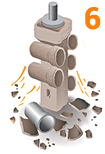
Knockout
The ceramic shell is broken off, and the individual castings are cut away.
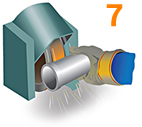
Finishing
Excess metal is removed, suefaces are finished, and castings are heat treated.
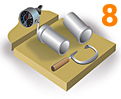
Testing and Inspection
Castings undergo thorough testing and inspection to ensure that they meet dimensional tolerances and specifications.
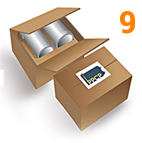
Packing and shipping
Castings are securely packaged for shipping to the customer.